滑動(dòng)軸承減摩層的電鍍新工藝(1)
(中國(guó)船舶重工集團(tuán)公司重慶躍進(jìn)機(jī)械廠 吳文俊)
[摘要]用正交試驗(yàn)法考察了滑動(dòng)軸承(又稱(chēng)軸瓦)減摩層電鍍液中有關(guān)成份的含量及工藝參數(shù)對(duì)鍍層性能的影響,使該電鍍工藝得到了進(jìn)一步優(yōu)化,顯著提高了鍍層質(zhì)量,滿足了主機(jī)廠新機(jī)型對(duì)滑動(dòng)軸承質(zhì)量的要求。
1 前言
在內(nèi)燃機(jī)中使用的滑動(dòng)軸承(又稱(chēng)軸瓦)是易損的關(guān)鍵零件。機(jī)械加工完畢后,一般在其內(nèi)表面的基體上先電鍍1~3μm厚的鎳(Ni)柵阻擋層[1~2],繼之電鍍15~30μm厚的鉛錫銅(PbSnCu)三元合金減摩層[3~24],最后在全部表面上電鍍1~2μm厚的錫(Sn)或鉛錫(PbSn)合金防護(hù)層[2]。
在軸瓦的內(nèi)表面提供減摩層的目的是為了提高軸瓦的減摩性、耐磨性、耐蝕性、鑲嵌性、順應(yīng)性、磨合性、抗咬合性、抗疲勞強(qiáng)度、抗壓強(qiáng)度、承載能力等,從而提高其工作性能,延長(zhǎng)使用壽命,最終保證主機(jī)的高性能運(yùn)行。
一般根據(jù)使用要求選擇鍍層種類(lèi)。小型發(fā)動(dòng)機(jī)的軸瓦一般使用PbSn6~20二元合金[12~13、16~17、22],也有使用鉛銅(PbCu)、鉛銀(PbAg)二元合金的。隨著時(shí)間的推移和科學(xué)技術(shù)的發(fā)展,對(duì)于大、中型柴油機(jī)、內(nèi)燃機(jī)上使用的軸瓦,要求具有負(fù)載能力大、使用壽命長(zhǎng),且應(yīng)具有良好的潤(rùn)滑性、耐蝕性、耐磨性等性能。實(shí)踐證明,在傳統(tǒng)的鉛錫(PbSn6~20)二元合金減磨鍍層中加入少量的第三組分元素銅(Cu)就可以顯著改善鍍層性能[3、10、20]。當(dāng)鉛錫(PbSn6~20)二元合金鍍層中加入2~3%的銅時(shí),一方面由于銅與錫具有一定的親合勢(shì),在一定程度上抑制了錫向襯里(即基體)擴(kuò)散,有利于保證鍍層中錫含量及其金相結(jié)構(gòu)的穩(wěn)定;另一方面,由于加入了銅后,鍍層的硬度從原來(lái)的HV8~10提高到HV13~15,大大改善了鍍層的耐磨性和抗疲勞強(qiáng)度等,從而顯著提高了軸瓦的負(fù)載能力,使用壽命大幅度延長(zhǎng)。
若在襯里金屬上直接電鍍減摩鍍層,則鍍層中的錫容易向襯里擴(kuò)散,使得軸瓦在工作一段時(shí)間后,鍍層內(nèi)的錫含量下降到小于6%(質(zhì)量)。并且無(wú)論是銅基合金襯里還是鋁基合金襯里,其中都含有一定量的銅,擴(kuò)散到襯里中的錫能與銅生成脆性大的金屬間化合物(Cu3Sn)。這樣不僅使鍍層的機(jī)械性能下降,而且破壞了襯里的結(jié)構(gòu),至使軸瓦的整體機(jī)械性能降低。解決該問(wèn)題的方法是在襯里材料與減摩底層之間電鍍一層鎳或鎳基合金阻擋層(又稱(chēng)柵層或阻擋層),以抑制錫向襯里擴(kuò)散[1~2]。
錫或鉛錫合金防護(hù)層除了具有一定的防腐蝕作用外,在軸瓦工作期間還可以擴(kuò)散的方式補(bǔ)充減摩層中的錫的含量,使其各成分的含量處于相對(duì)穩(wěn)定的狀態(tài)。另外,由于這層防護(hù)層不含銅,相對(duì)較軟,因此軸瓦在工作的初期就能達(dá)到良好的磨合要求。
本文主要考察軸瓦減摩層的電鍍工藝。
2 發(fā)展歷程
減摩鍍層在國(guó)外的研究起步較早。1920年由格羅奧夫(J.Grooff)提出了電鍍鉛錫合金的第一個(gè)專(zhuān)利,并用于海軍魚(yú)雷儲(chǔ)氣瓶的內(nèi)表面電鍍,到二十世紀(jì)四十年代開(kāi)始用于軸瓦的電鍍。1952年舒爾茨(Schults)提出了在鋁及鋁硅(AlSi)合金基體上電鍍鉛錫銅三元合金的專(zhuān)利。1953年舍夫(Schoefe)曾發(fā)表軸瓦使用鉛錫銅合金的綜述。1976年,Jong—Sang Kim,Su—ιι Pyun and Hyo—Geun Lee發(fā)表了“鉛錫銅電鍍層的晶面取向及微觀形貌”的論文[7]。1980年畢比(Beebe)提出含銅2~3%(質(zhì)量)、錫9~12%(質(zhì)量),其余為銅的三元合金電鍍生產(chǎn)工藝流程,鍍層厚度為15μm。1982年沃特曼(Waterman)等人就三元合金電鍍液中銅離子(Cu2+)的置換問(wèn)題提出了解決的辦法。
國(guó)內(nèi)對(duì)于減摩合金鍍層的研究和應(yīng)用起步較晚。1960年初,武漢材料保護(hù)研究所與海陵第一配件廠首先研制并用于生產(chǎn)的電刷鍍鉛錫合金工藝已用于快艇發(fā)動(dòng)機(jī)的電鍍。二十世紀(jì)七十年代中期,上海合金軸瓦廠及上海滬東造船廠對(duì)軸瓦電鍍銅錫合金工藝者了較詳細(xì)的研究[12~13]。1985年,哈爾濱工業(yè)大學(xué)電化學(xué)教研室與中國(guó)船舶工業(yè)總公司四六六廠共同研究了鉛青銅滑動(dòng)軸承上電鍍鉛錫銅三元合金減摩層的工藝,并已用于生產(chǎn)。1989年,Dusanka Radoric發(fā)表了“在氟硼酸鹽鍍液中以氫醌(對(duì)一苯二酚)為添加劑的鉛錫合金電鍍”的論文16。十十世紀(jì)末,南通軸瓦廠的范家華、姜志東21、24,武漢材料保護(hù)研究所的曾良宇、楊先桂、王會(huì)文8、17,廣西桂林內(nèi)燃機(jī)配件廠的秦勝毅9,戚墅堰機(jī)車(chē)車(chē)輛工藝研究所薛伯生20等對(duì)減摩層的電鍍工藝從不同的方面先后進(jìn)行過(guò)不同程度的研究,為該工藝在生產(chǎn)應(yīng)用中的進(jìn)一步完善奠定了一定的基礎(chǔ)。
3 問(wèn)題的提出
我廠的鉛錫銅三元合金減摩鍍層的電鍍工藝屬?lài)?guó)內(nèi)首創(chuàng),多年來(lái)為我國(guó)主機(jī)配件市場(chǎng)提供了大量軸瓦。近年來(lái),我廠軸瓦產(chǎn)品定貨量逐年上升,并且有些軸瓦產(chǎn)品已打入國(guó)際市場(chǎng),具有一定量的出口。這充分體現(xiàn)了我廠的軸瓦產(chǎn)品在激烈的市場(chǎng)競(jìng)爭(zhēng)中具有相當(dāng)強(qiáng)的實(shí)力。
自1989年到1991年期間,通過(guò)我們的艱苦努力、反復(fù)試驗(yàn),已從根本上解決了軸瓦鍍層起泡、脫皮等附著強(qiáng)度差的致命缺陷問(wèn)題;消除了基體遭受批量性嚴(yán)重腐蝕的故障;克服了批量性壁厚超差,提高了工序能力;廢品損失率一直很低,一次交檢合格品率逐年提高。
然而,鍍層粗糙、結(jié)瘤、花斑、凹坑、氣流條紋等缺陷還時(shí)有發(fā)生,有時(shí)還出現(xiàn)陰極電流密度(DK)達(dá)不到工藝范圍的現(xiàn)象。
減摩鍍層的上述缺陷直接影響軸瓦產(chǎn)品質(zhì)量。隨著主機(jī)廠機(jī)型的不斷更新?lián)Q代、進(jìn)口機(jī)型的國(guó)產(chǎn)化及市場(chǎng)競(jìng)爭(zhēng)的日趨激烈,用戶對(duì)軸瓦產(chǎn)品質(zhì)量的要求越來(lái)越高。市場(chǎng)的競(jìng)爭(zhēng)從根本上說(shuō)就是產(chǎn)品質(zhì)量的競(jìng)爭(zhēng)。在用戶對(duì)產(chǎn)品質(zhì)量指標(biāo)要求日益提高的形勢(shì)下,我們面臨著改進(jìn)軸瓦電鍍工藝、進(jìn)一步提高軸瓦產(chǎn)品質(zhì)量這一新課題的嚴(yán)峻挑戰(zhàn)。
- NNCF4832CV軸承_SKF
- RS-4956E4/RSF-4956E4軸承_NSK
- 6013NR軸承_NACHI
- 23230BK+AHX3230軸承_NTN
- 24030-E1-K30軸承_FAG
- 51240軸承_KOYO
- CR32X47X7HMSA10RG軸承_SKF
- AWL24/AWL24X軸承_NSK
- NKS70軸承_FAG
- 32210JR軸承_KOYO
- 23040CCK/W33軸承_SKF
- NU209E/NJ/NUP軸承_NTN
- 7007-B-2RS-TVP軸承_FAG
- HK3038軸承_SKF
- 49175/49368軸承_TIMKEN
- 239/710EW33K軸承_NACHI
- LRT81011軸承_IKO
- GE16-DO軸承_FAG
- NUP340軸承_NACHI
- C30/1000MB軸承_SKF
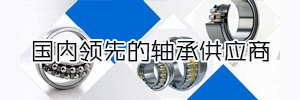